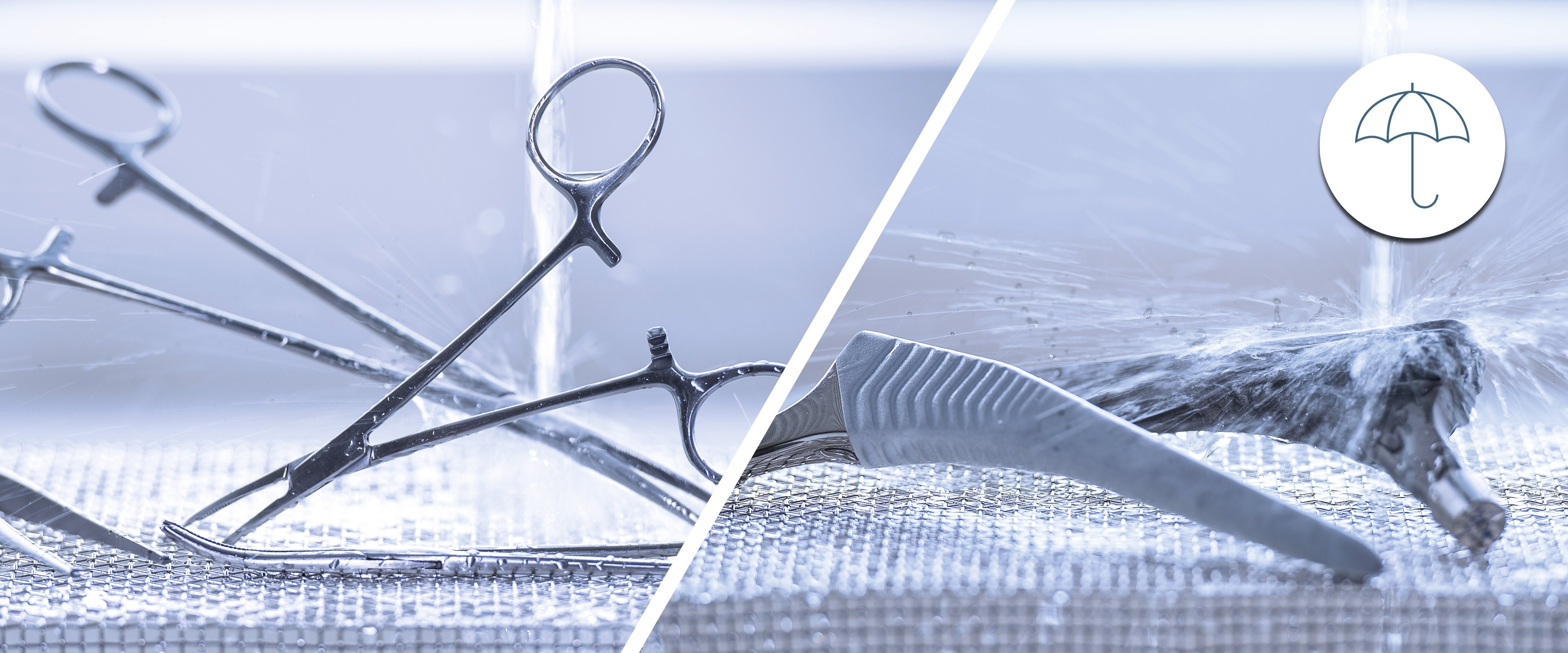
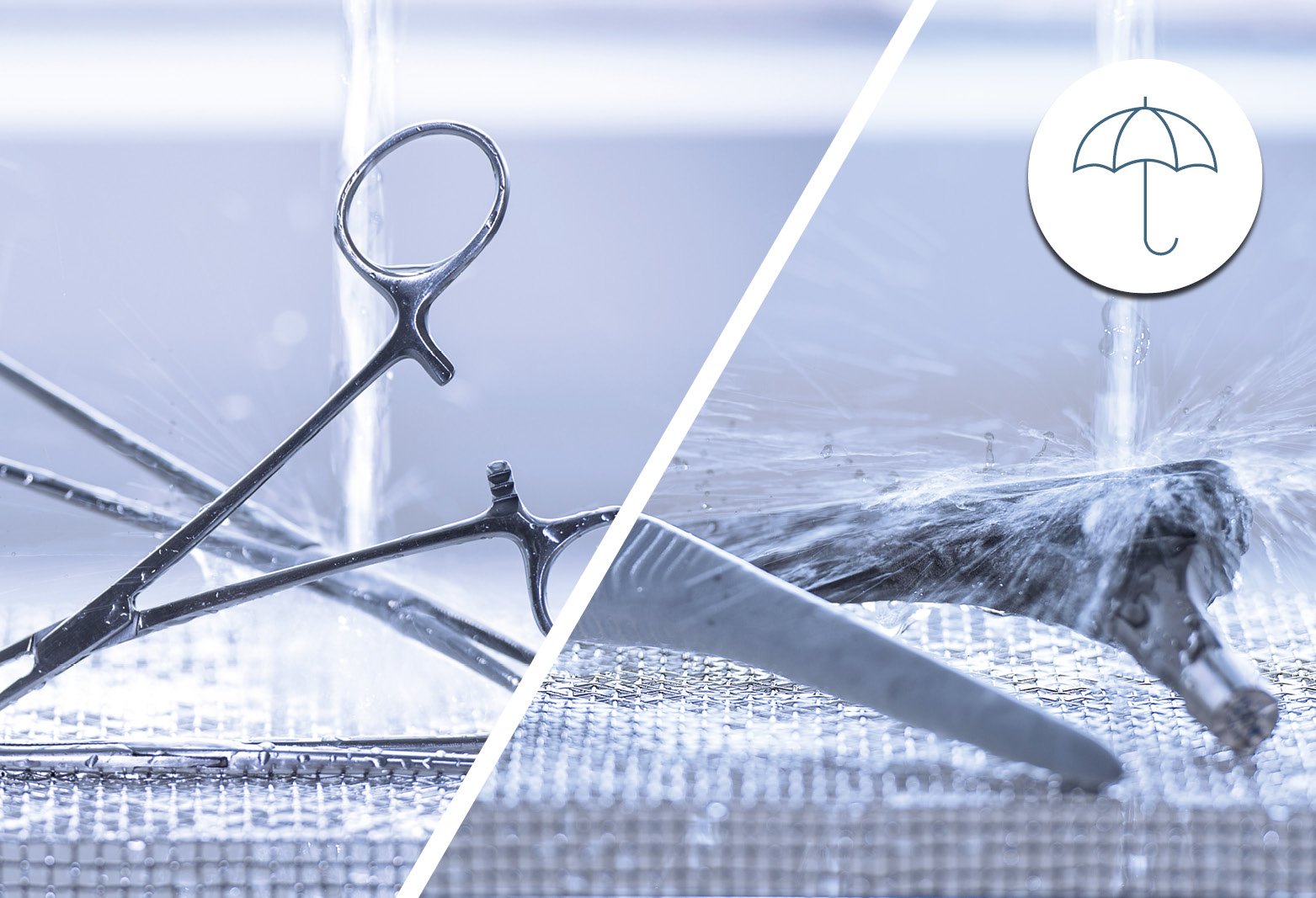
Successful passivation begins with the right preparation
You don‘t hear it coming, it isn‘t immediately visible, it happens insidiously and every production manager is happy if it doesn‘t set in: we‘re talking about unwanted oxidation (rust). With a combination of the right system technology and the innovative passivation method developed by Borer Chemie AG, products can be effectively protected during? the manufacturing process.
Ensuring resistance to corrosion on metal materials is essential for avoiding undesired oxidation. The long-term legibility of product markings for complete traceability and permanent resistance to corrosion are guaranteed with this passivation method. Complex shapes, demanding materials and new technologies such as additives, pose a particular challenge for production.
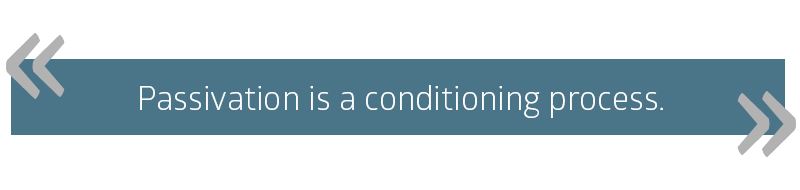
What exactly is passivation
Often, the process is associated with surface protection such as coating (anodising, burnishing, etc.), a layer of oil on the metal surface or similar applications. This application has nothing to do with the actual passivation process, however! Passivation is a conditioning process. In surface technology, this means that a protective layer forms spontaneously or is generated deliberately on a metallic surface through the use of the correct medium, e.g. deconex® MT 41. This protective layer prevents corrosion of the base material or significantly slows it down.
The importance of pre-cleaning
Metallic products that must guarantee long-lasting protection for their future use are chemically passivated. Before passivation, however, it is essential to create a clean and residue-free surface. High-quality preliminary cleaning is therefore so important because the passivation media will only be able to trigger a reaction at the places where direct contact with the metallic surface can be guaranteed. Long-lasting protection cannot be guaranteed even with passivation if the surface is not clean before the passivation process.
The 7-step cleaning concept
Borer Chemie AG has developed its own deconex® cleaning concept for its customers, including passivation for the high demands of the production process. This can be used on different system technologies such as immersion or spraying, but also with the new vacuum process. The cleaning concept is based on a structured, 7-step procedure in which the customer's requirements are documented and used to develop a cleaning and passivation method optimised to the customer's specific needs.
7-step procedure towards structured process development
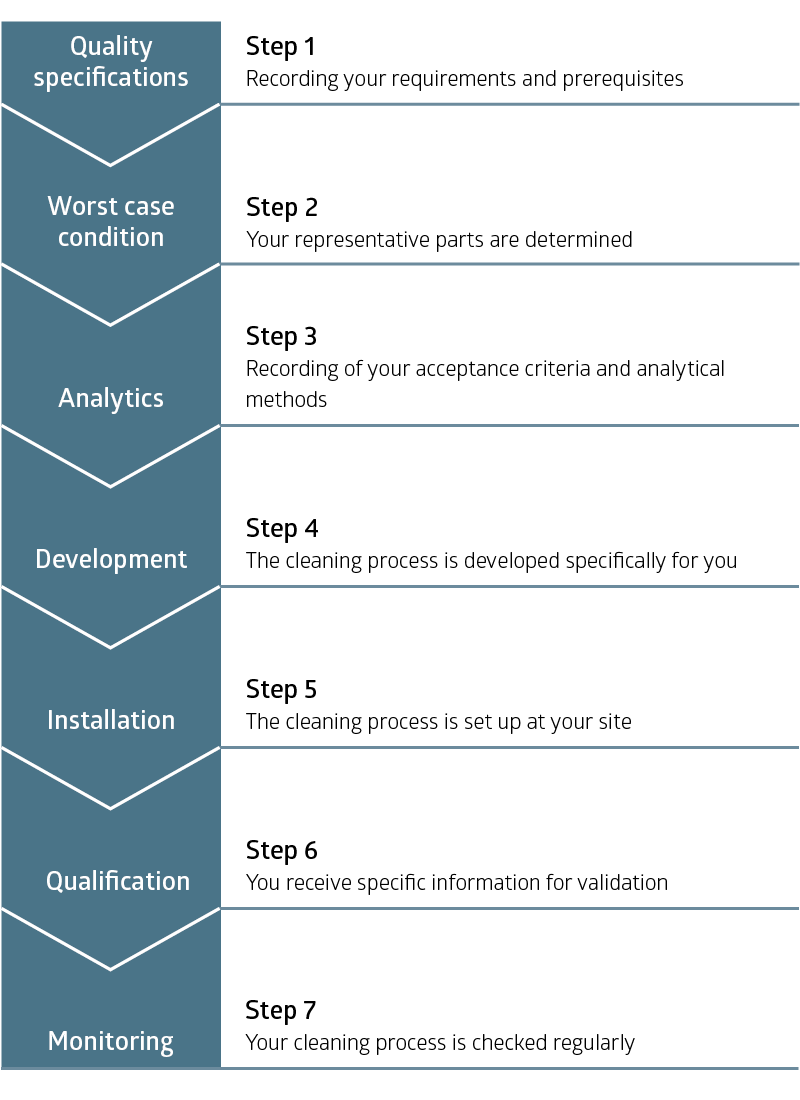
For the most demanding situations
deconex® cleaning agents take into account manufacturers' high standards and are developed on a customer-specific basis to be implemented at the customer's site. Depending on the industry, undesirable ingredients that are difficult to rinse off are completely dispensed with. This significantly reduces the risk of contamination from process media on the one hand, and on the other ensures process reliability since residue (process chemicals and production residue) can be removed very effectively. Ultimately, the process delivers reproducible results.
he deconex® product portfolio is rounded off with the new passivation method which shows better results compared to the conventional nitric and citric acid methods well known on the market.
Test your processes and our deconex® cleaning agents on various types of equipment in our test and training centre, which is unique in Europe.
The deconex® MT 41 passivation solution
deconex® MT 41 is a highly acidic passivation agent with a pH of 2.2 containing phosphoric and nitric acid as well as non-ionic surfactants.
The advantage of this passivation solution lies in the fact that, compared to immersion passivation with nitric acid (HNO3), it can be used at significantly lower concentrations. Thanks to the lower concentration of 0.02 to 0.12% vol., deconex® MT 41 can be used for conventional immersion passivation as well as for the new, more economical method of spray passivation and especially for passivation using under vacuum. The temperature range extends from 20 to 85°C. High temperatures are essentially important for the efficiency of the passivation process since chemical reactivity increases at higher temperatures. Conventional passivation processes based on nitric acid cannot be used under vacuum or spray methods due to the temperature variables, gas formation and foaming behaviour. Safe use would be unlikely.
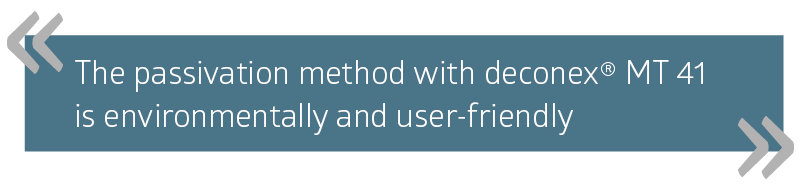
Generally speaking, the novel passivation solution can be used successfully for the passivation methods mentioned (spray, immersion and vacuum) thanks to its tiny concentrations.
Compared to conventional immersion passivation with nitric acid, the passivation method with deconex® MT 41 is not only more economical, but it is also more ecological and user-friendly.
The solution is biodegradable and, thanks to its low concentration, can be disposed of via the normal wastewater system if local wastewater regulations permit this.
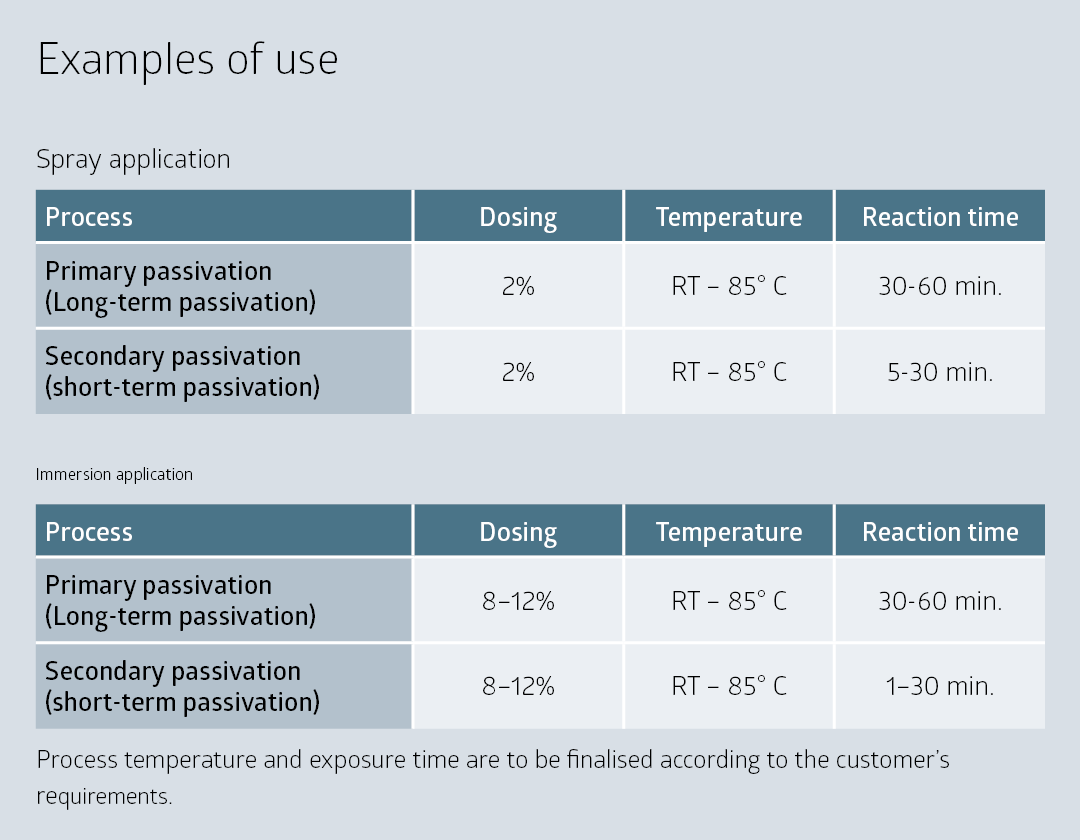
A passivation process with measurable added value
The passivation process developed by Borer Chemie was compared with other passivation media from an economic and ecological perspective, as well as in terms of material compatibility, and delivers measurable added value. Passivation with deconex® MT 41 was also compared with conventional passivation methods from the point of view of the formation and extent of the oxide layer. This resulted in the following findings:
The illustration shows that an very high ratio of Cr-Fe and Cr oxide - Fe oxide has formed on the surface compared to the application involving nitric / citric.
The results achieved with deconex® MT 41 can also be used as reference for welding seams, which are comparable in principle to additive manufacturing.
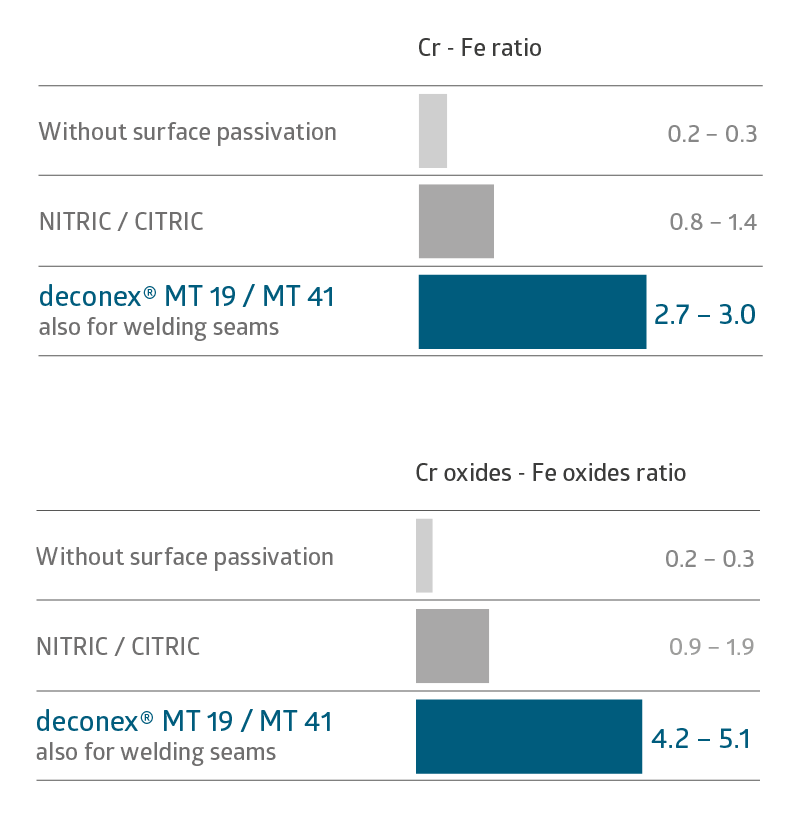
The benefits of a correct application of the passivation process
+ Removal of foreign metal impurities ("metallic purity")
+ Extending the life of metallic products
+ Biocompatible surfaces through passivating oxide layer
The advantages of deconex® MT 41 compared to nitric acid
Nitric acid is a tried-and-tested process medium which ensures passivation of the metal surface. Its advantages and disadvantages are well-known:
it is recognised, for example, that a good formation of the oxide layer is guaranteed and that the process is approved in medical technology, for example, according to the ASTM A987 standard. The known disadvantages of nitric acid include the loss of contrast on labels and, as a consequence, reduced legibility, the formation of nitrous gases,
a high concentration of chemicals and laborious wastewater and exhaust air handling routines. In all of these cases, the use of deconex® MT 41 brings added value to the passivation process.
The comparison of the nitric acid and deconex® MT 41 passivation media shown below highlights the advantages of using deconex® MT 41:
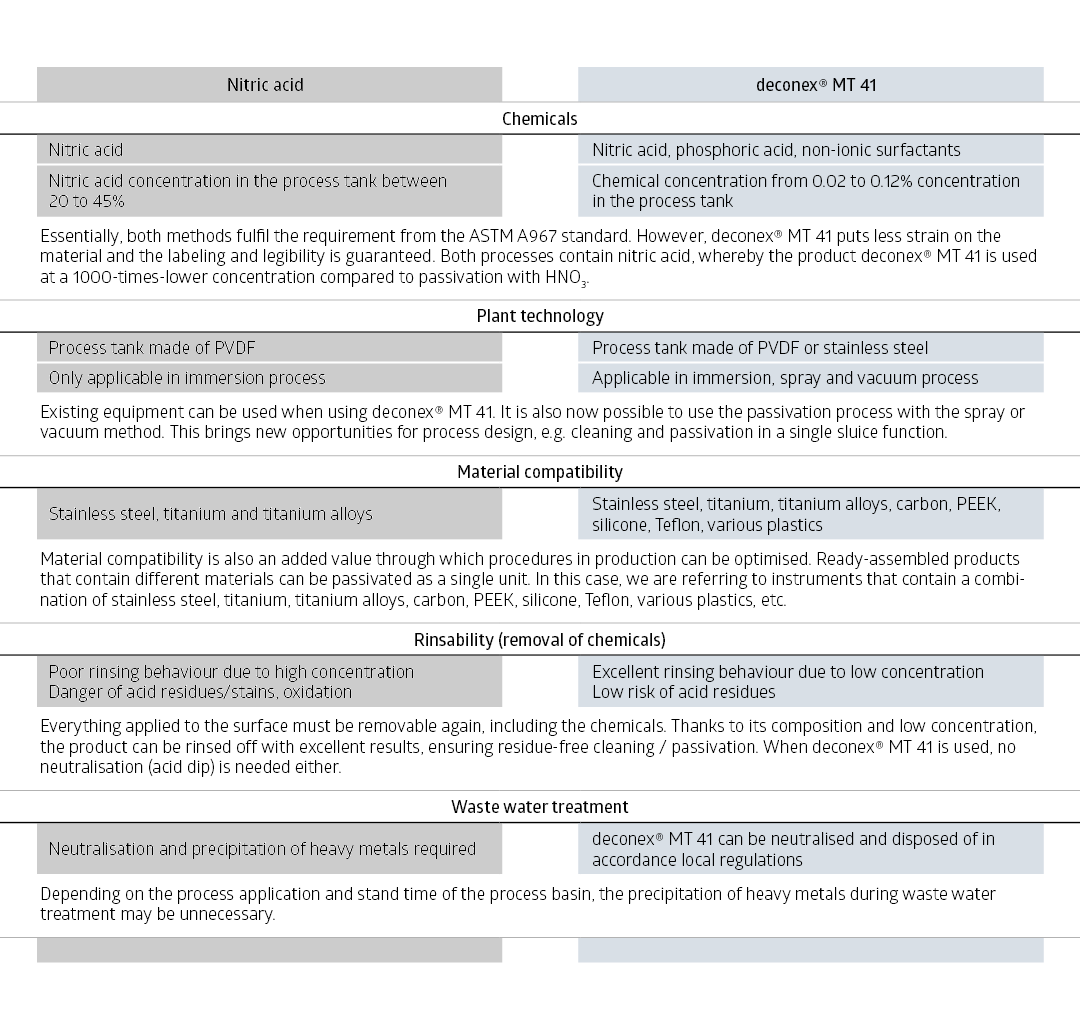
New possible applications and advantages in the passivation process
• Application with the spraying processes
• High/broad material compatibility
• Application at low concentrations
• Very low nitrous gas formation
• Cleaning and passivation is possible in the same working chamber (spray application)
• Can be used in a material sluice airlock (tunnel) function
The most important in brief
The passivation process from Borer Chemie AG is using a 1,000-times lower concentration of acid than conventional methods. Nevertheless, a thicker inert layer is quickly formed which ensures that the products are protected from possible corrosion.
Laser marked labels and their contrast are less stressed by passivation with deconex® MT 41, so legibility with the naked eye remains guaranteed.
deconex® MT 41 is biodegradable and does not require the handling of precipitates (heavy metals) which may occur in the conventional methods. The used solution can also be easily neutralised and disposed of in accordance with the law.
Alongside conventional immersion baths, the passivation method can also be used in closed spray cleaning systems or in processes, which are using vacuum. This opens up entirely new possibilities in production processes and the associated zone concepts.
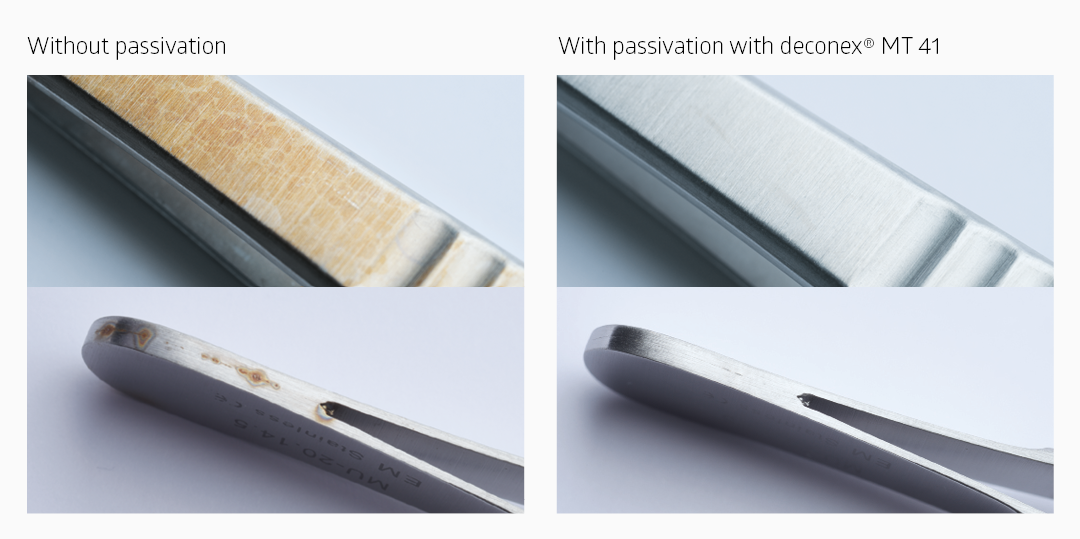
Get in contact!
Do you have questions about our products and services? Contact us!