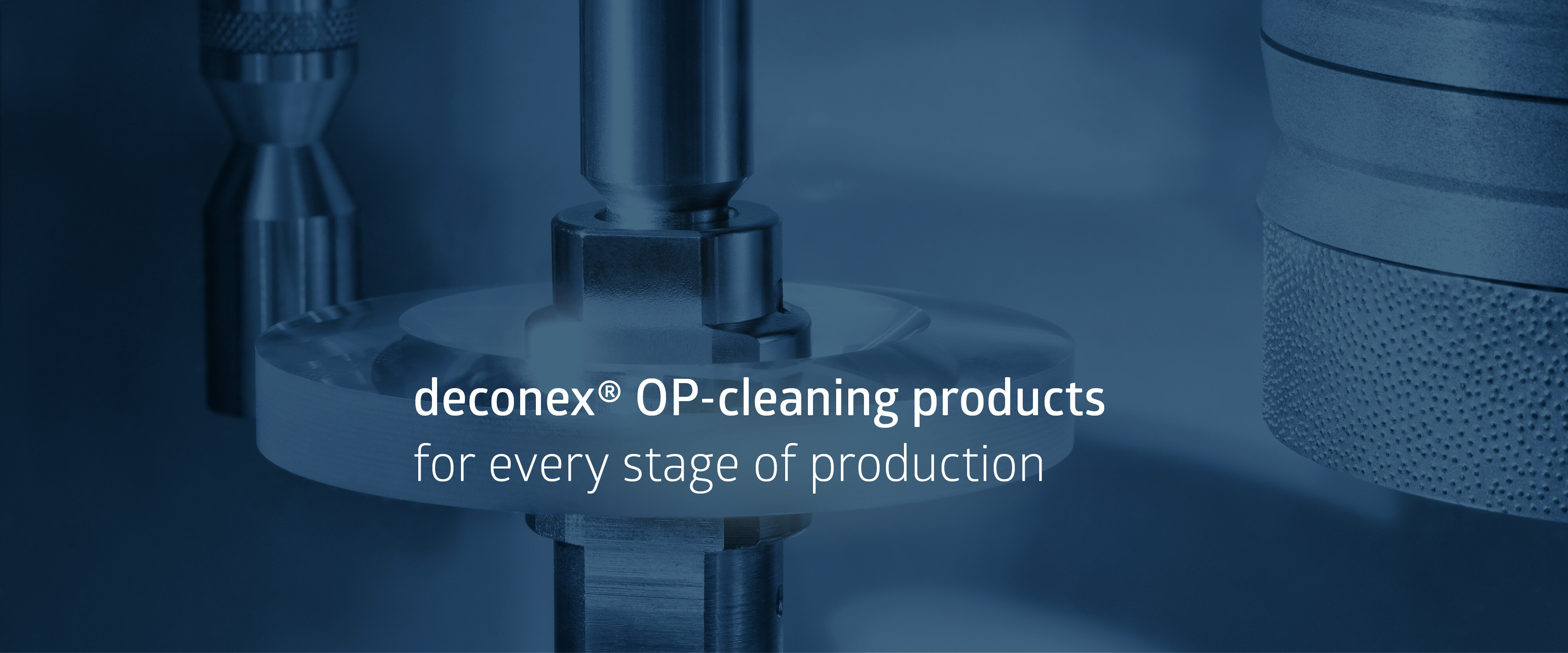
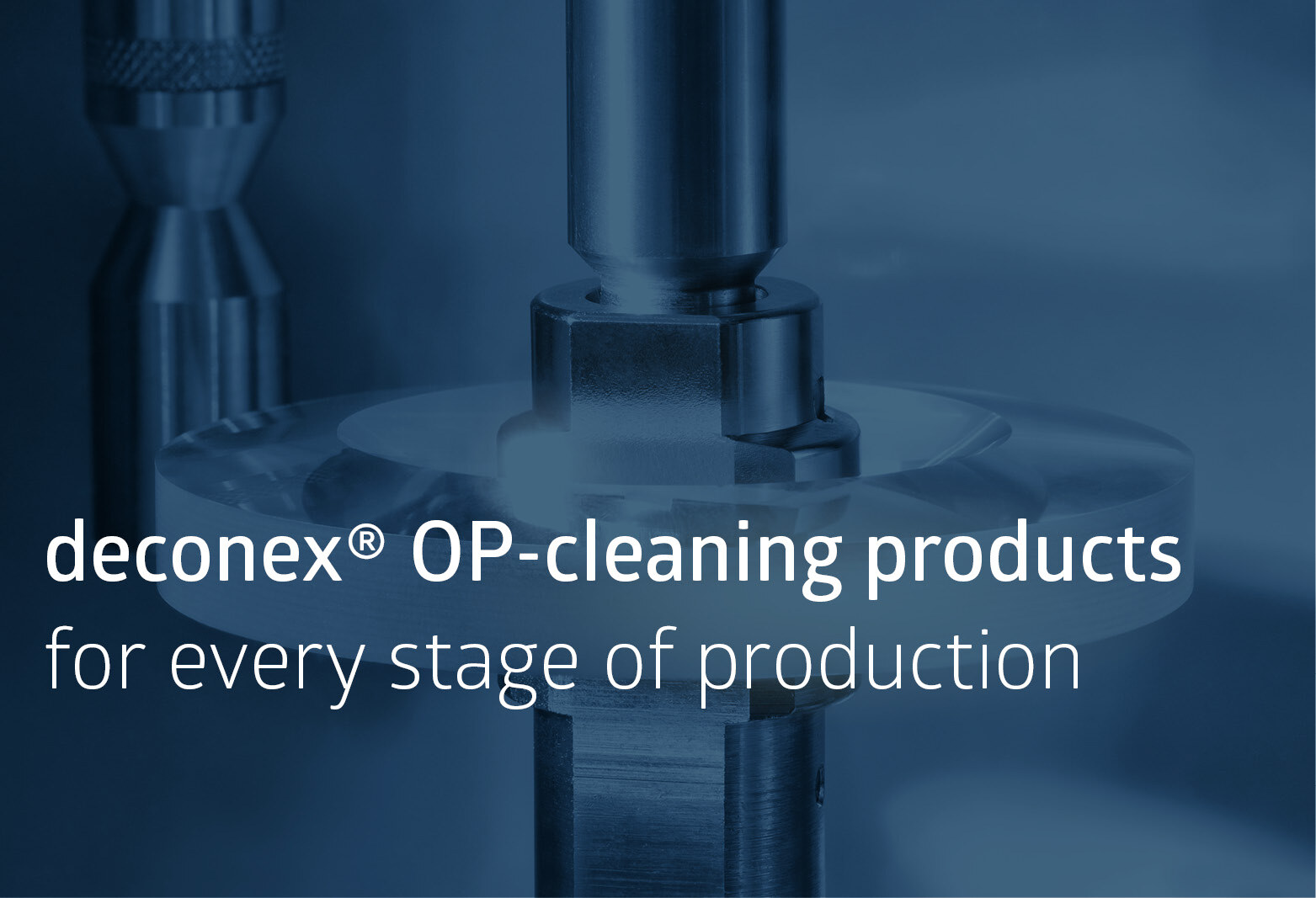
High-performance products for residue-free cleaning in the production of ophthalmic lenses and optoelectronics
We have a clear view
With decades of experience and in-depth expertise in the optical industry, we fulfil the highest standards of cleanliness. Our deconex® cleaning solutions are optimised to meet the needs of our customers, both in terms of system technology and chemical properties.
This enables us to achieve the best possible coating and decoating results for highly sensitive and acid-sensitive glass as well as for optical components made of various types of glass or plastic.
The Borer complete package:
products and services
- Specially developed products for
the specific requirements of the optical industry - Suitable for organic, mineral and precision optical glasses
- Processes for activating surfaces and for achieving residue-free surface cleanliness
- Applications and process parameters for a wide range of system technologie
- Expertise and knowledge transfer from process development to implementation
Download product brochure
Contact us for advice on our products and services. Our process specialists will be pleased to help!
Cleaning is the basis for flawless quality
In the manufacturing of ophthalmic lenses, it is crucial that each process step fulfils the highest cleanliness requirements and that no impurities are carried over. We have analysed these processes in detail and identified the process steps in which the highest cleaning requirements must be met in order to achieve optimum results.
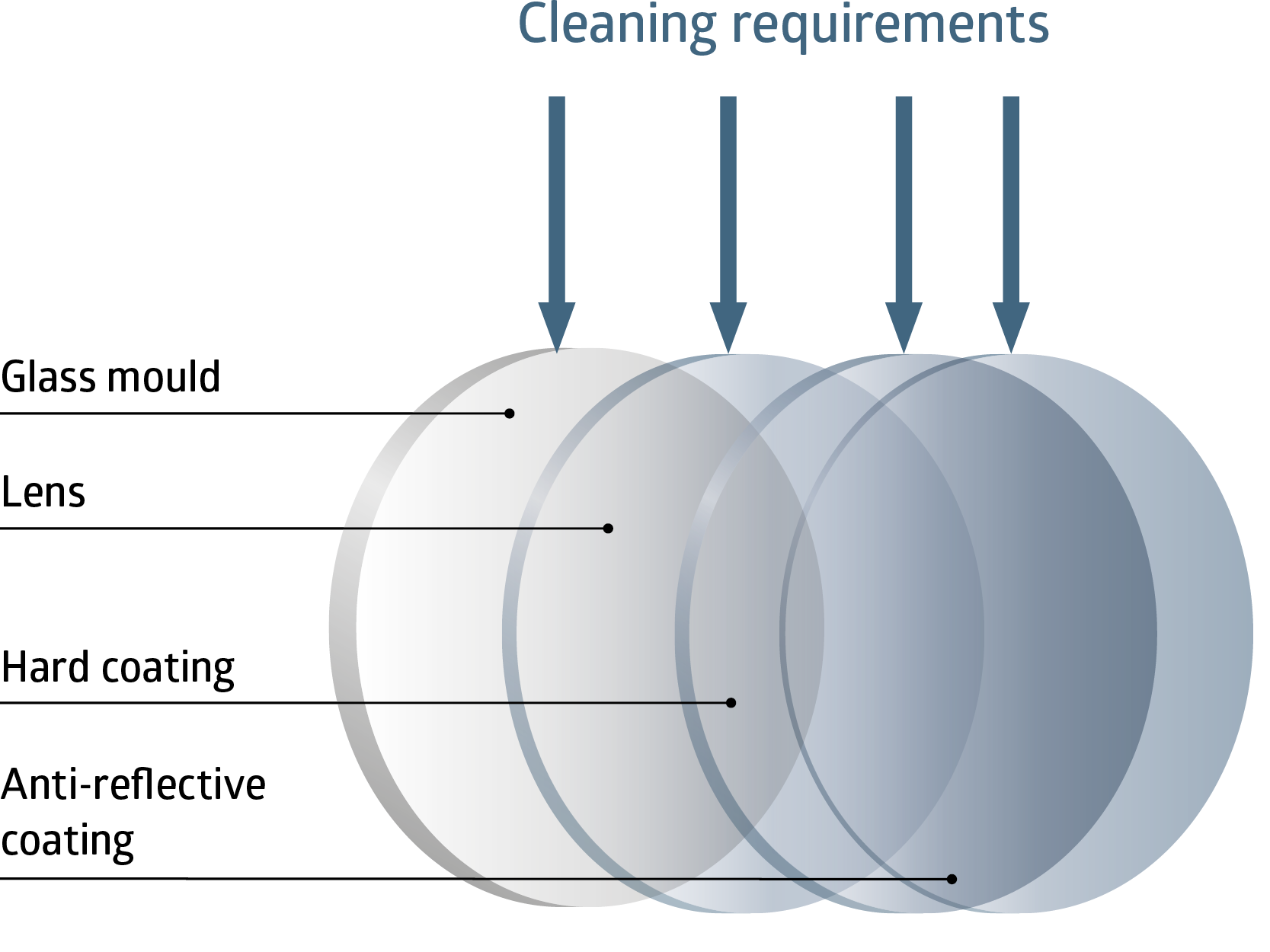
We specialise in the cleaning of glass moulds as well as cleaning between the various stages of lens production, particularly before hard coating (HC) anti-reflective (AR) coating.
HC and AR coating are the most cost-intensive steps in the entire lens production process, so ensuring the highest surface cleanliness and hard coating adhesion by activation of the surface is crucial. Our focus on purity and quality guarantees you clear and brilliant results ensuring that your ophthalmic lenses not only meet the highest standards, but also increase the cost efficiency of your entire production and fully fulfil the quality requirements of your customers.
deconex® OP cleaning solutions for every stage of production
The products in the deconex® OP line have been specially developed for use in pre-cleaning ready for inspection and in fine cleaning ready for coating. Here they are used for the removal of
- polishing pastes
- colour markings
- lacquers
- protective film residues
- fingerprints
- dust and all kinds of particles
We also offer a customised solution for coating defects with the deconex® de-coat product line. The decoating solutions efficiently and effectively remove defective anti-reflective and hard coating layers ready for recoating. Our experts also support you in cleaning spectacle frames as well as glass moulds and thermoplastics.
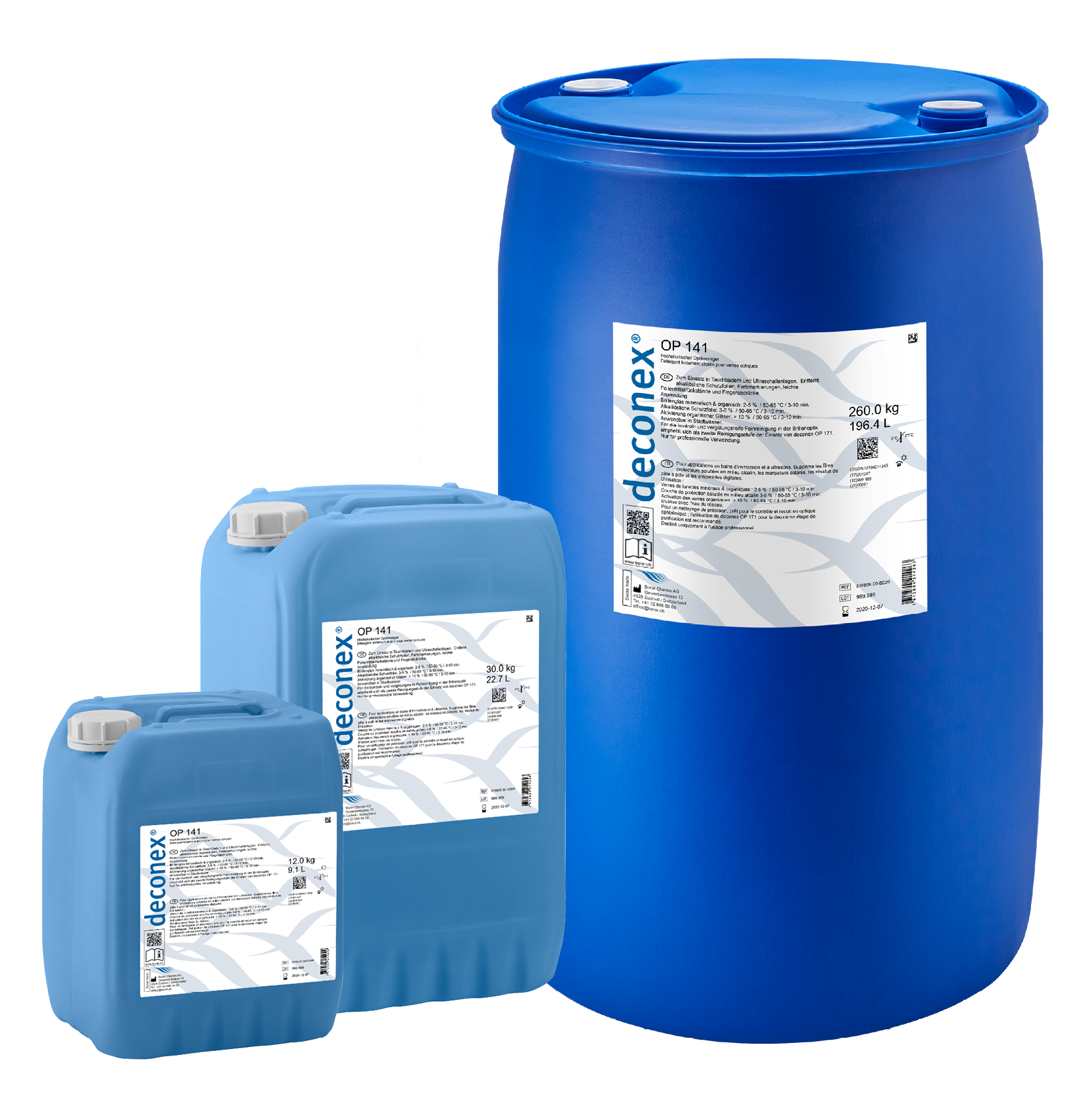
Our solutions in the manufacturing process for ophthalmic and sunglass lenses
In order to ensure consistent quality and precision of the manufactured parts, the correct cleaning and decoating steps are of crucial importance in ophthalmic lens production.
The flow chart shows at which point in the manufacturing process these should be incorporated:
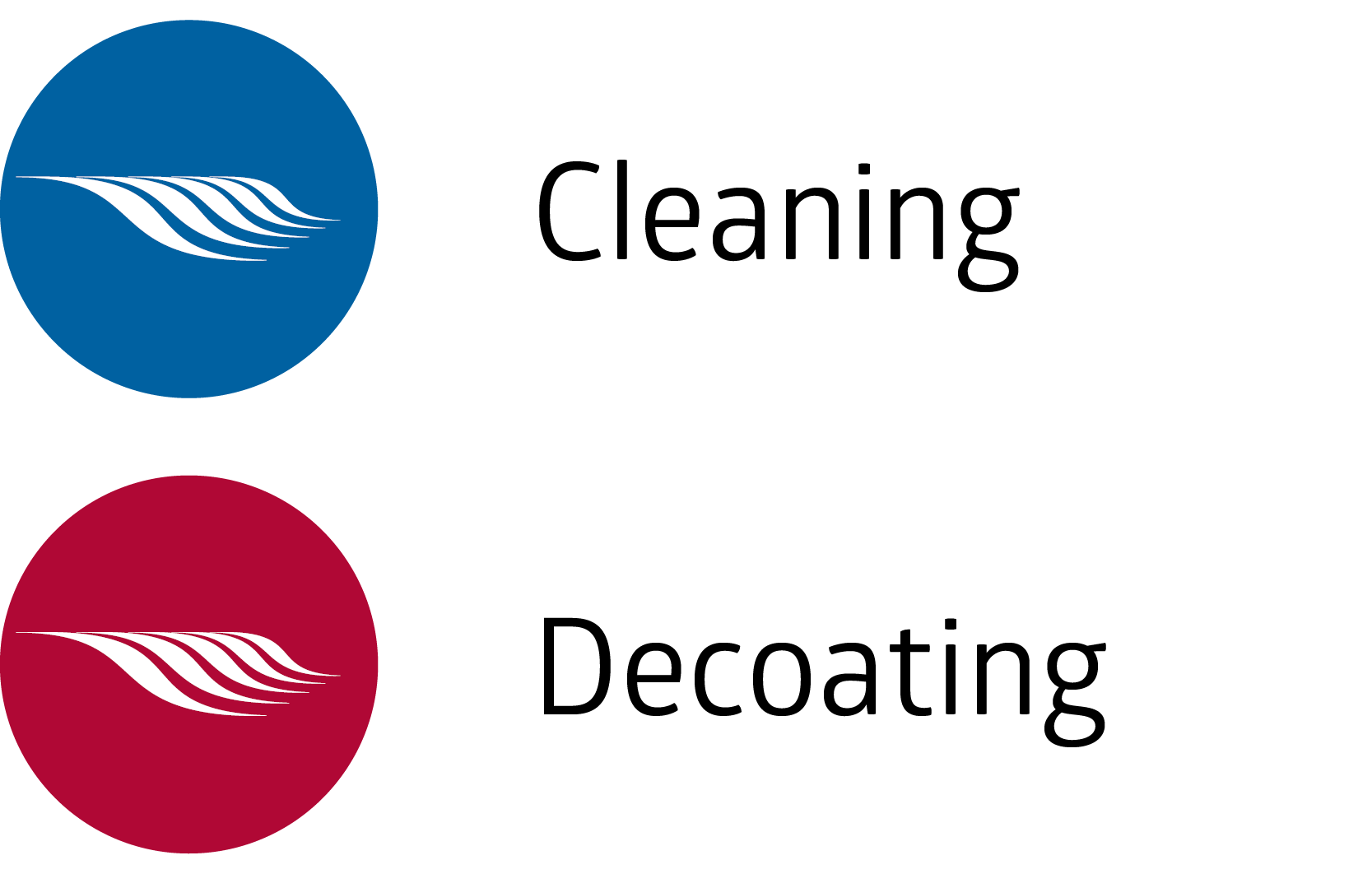
In our deconex® portfolio you will find suitable products for every application in the cleaning and decoating of ophthalmic and sunglass lenses.
Meticulous purity in optoelectronics
The production of optoelectronics demands the utmost precision to guarantee excellent quality and performance, meeting the standards of modern technology. Ensuring that no impurities or particles remain on the surface of the lenses or on the cover slips is essential, as even the slightest particles could substantially hinder the optics’ performance.
Our tried-and-tested deconex® cleaning solutions have been specially developed to remove precisely this type of contamination. They are used, for example, in the cleaning of cover slips used in the production of image sensors.
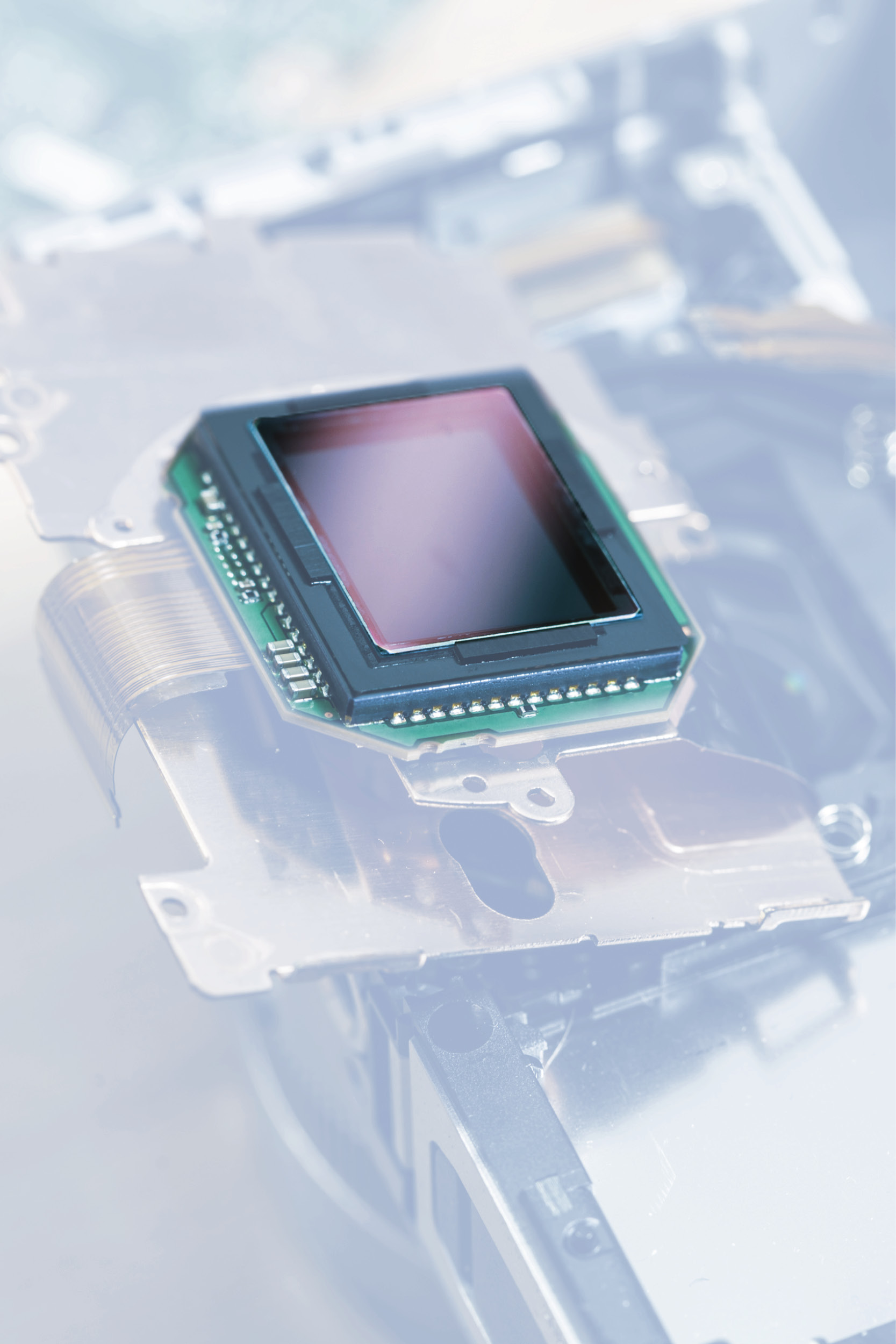
Four steps to reproducible cleaning
results:
1. Cleaning the bare glass after machining
After the glass has been cut, ground and polished, careful cleaning is necessary to remove all production residues and impurities.
2. Cleaning the bare glass before AR coating
Before applying the anti-reflective coating, the glass is cleaned again to ensure that the coating adheres to a clean surface.
3. Cleaning AR-coated glass before dam coating and after structuring
The AR-coated glass undergoes further cleaning steps to maintain cleanliness during the complex production processes.
4. Cleaning AR and dam-coated glass before attaching the silicon sensor
This step is crucial to ensure that the sensor chip encounters a perfectly clean surface.
At the end of the manufacturing process, the cleaned cover slip with AR and dam coating is precisely applied to the sensor and then cut into individual modules.
The primary objective when inspecting the cover slip after cleaning is to ensure that no particles or residues > 5 μm in size are present. Such particles could impair the incidence of light in the sensor chip, leading to deflections or unwanted reflections of the light. This reduces the amount of light transmitted to the sensor component and results in a lower resolution.
Our contribution to your success story
Customer service from A to Z
Your specific cleaning tasks are in the best hands with us! As experts with decades of experience, we support you in solving all your cleaning tasks. You can rely on us as a neutral partner with a large network of cooperation partners and market leaders.
Whether you are already using our deconex® products or just want to get to know them: you benefit either way from our comprehensive advice and a wide range of services.
Working closely with your experts, our cleaning specialists develop specific cleaning processes tailored to your needs. We also support you with on-site implementation and qualification, as well as with the regular monitoring of the ongoing process.
tests
tests
services
services
The Borer Test and Training Centre
First test, then implement
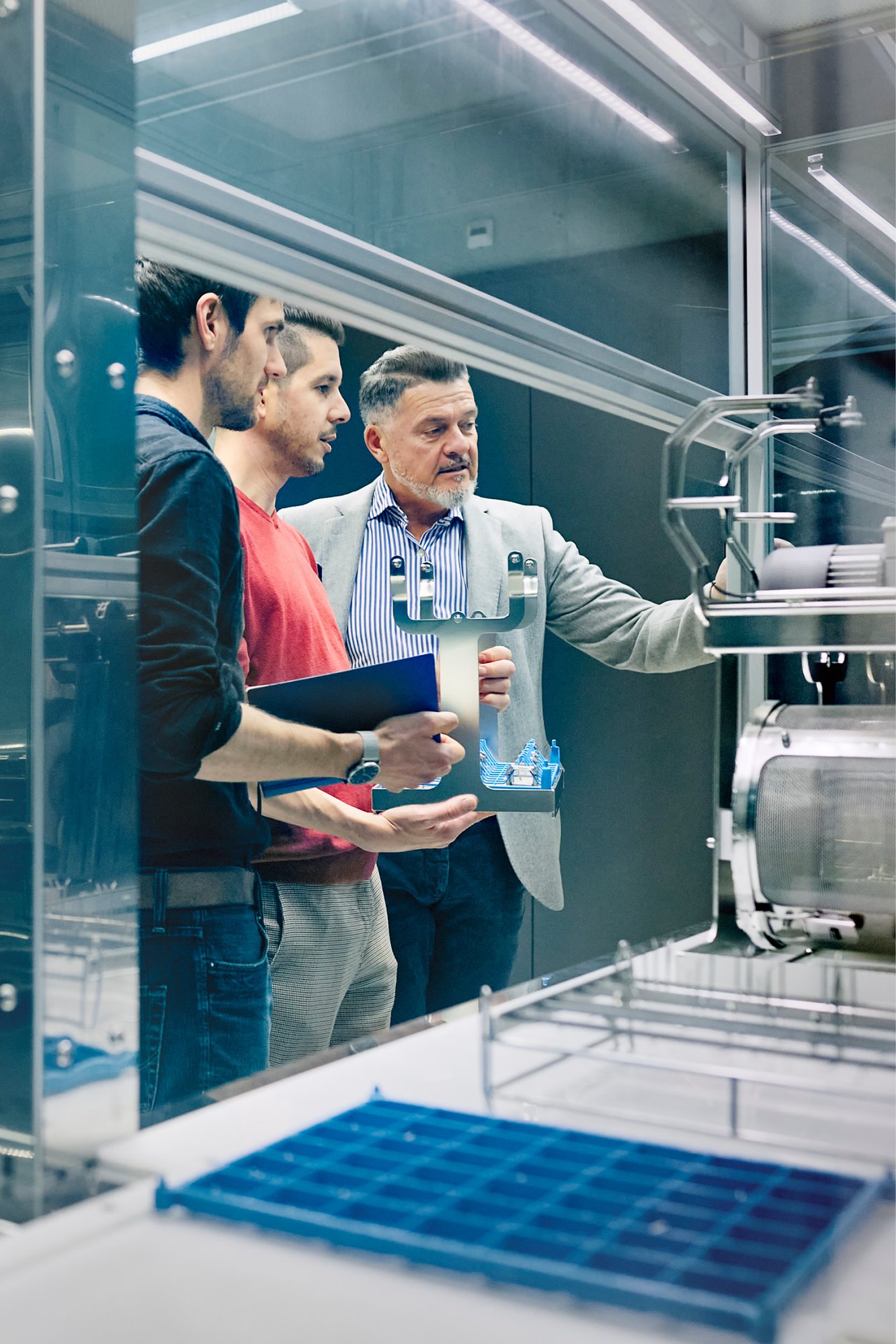
The development of complex cleaning processes requires not only extensive experience, but also a thorough testing programme.
Explore the future of customized cleaning, passivation and decoating processes at our state-of-the-art Training Centre located at our headquarter in Zuchwil and test potential system technology and chemistry under real conditions before making investment decisions.
As your dedicated partner, we guide you through root-
cause analysis and develop and refine your processes on realistic production lines. Our comprehensive services include an in-house chemical laboratory, research and development, and process simulations across diverse industrial fields, such as:
- Optics (deconex® OP)
- Precision metals (deconex® HT)
- Watch industry (deconex® HT and deconex® OP)
- Tools/mould manufacturing (deconex® HT and deconex® MC)
- Vacuum and semiconductors (deconex® HPC)
- Medical technology (deconex® MT)
Contact
Do you have any questions about our products and services? Please contact us!